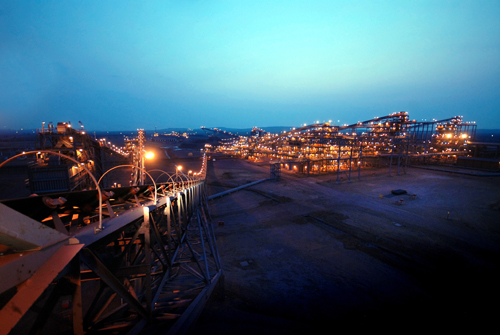
Originally known as The Associated Manganese Mines of South Africa Limited, Assmang as it exists today bears very little resemblance to the fledgling company that started work on the Northern Cape’s manganese fields in 1935. Today, the three operating divisions benefit from the modern mining infrastructure and technologies, while Assmang’s “we do it better” philosophy has helped to ensure low operating costs and high employee buy-in.
The company has retained its flexibility, developed over decades of hardship in difficult operating conditions, which is helping Assmang to enter a new phase in its challenging but often distinguished history with confidence, even in the face of tough global market conditions and challenges.
Assmang currently has three operating divisions based on its three commodities namely chrome, manganese and iron ore. Although each division operates independently, together they strive to achieve optimum efficiencies.
Assmang's manganese ores and alloys consists of the manganese mines in the Northern Cape Province of South Africa, namely N’Chwaning and Gloria mine, and the ferromanganese works at Cato Ridge in the KwaZulu-Natal province. The company’s chrome ores and alloys consist of the Dwarsrivier chrome mine and the Machadodorp ferrochrome works both in the Mpumalanga Province, while its iron ore is made up of the high grade Khumani Mine and the Beeshoek Mine both situated in the Northern Cape Province, around the towns of Kathu and Postmasburg. While Assmang is very much a medium sized player within the global market it is a very important one, particularly as it holds the distinction of being South Africa’s second largest iron ore producer. Nevertheless the domestic market takes only a small proportion of its output, with 40 percent of what it exports annually through the port of Saldanha shipped to China, with Korea, Japan and Europe sharing the remainder.
The Khumani iron ore mine, formerly known as the Bruce, King and Mokaning (“BKM”) Project which refers to the farms on which the iron ore resources are located, is situated approximately 30 kilometres south of the town of Khatu, in the Northern Cape Province of South Africa and approximately 65 kilometres north of Beeshoek Mine.
The Khumani iron ore mine has been designed to produce ten million tonnes of export quality iron ore each year, a figure that will eventually rise to 16 million tonnes upon completion of phase 2 of the Khumani Expansion Project. The Phase 2 expansion includes the development of the mining platform on the King property, material handling systems, stockpiles, stackers & reclaimers, a local railway siding, an additional rapid load-out station, a paste disposal facility, haul roads and other supporting facilities. The iron ore mined, at the Khumani iron ore mine, will initially only be exported, however with future expansions it will also cater to the local South African steel market.
The ore at Khumani is close to the surface, and it is a very high grade deposit, with a stripping ratio of 1.7 to 1. This means 10 units of iron ore for every 17 units of material excavated, and the iron ore, a high proportion of which is described as ‘lumpy’, in turn yields 66 percent iron. The Khumani resources are amongst the best iron ore resources in South Africa in terms of quality and quantity. It is estimated that the reserves will keep the mine going for more than 25 years at an annual extraction rate of 16 million tonnes.
The iron ore is mined from a series of open pits, on the Bruce and King properties, by means of conventional drilling, blasting and loading into trucks for hauling to each of the Bruce and King primary and secondary crushing facilities. From there, it is transferred by means of overland conveyor and stockpiled onto blending beds that separate the material into two categories, on- and off-grade material, ahead of treatment at the Parsons Beneficiation Plant.
On-Grade material is moved from the on-grade stockpile through to the washing and screening plant situated on the Parsons property, to ultimately produce final product incorporating tertiary crushing of any oversize material from the screening plant.
Off-grade material on the other hand is moved from the off-grade stockpile through to the washing and screening plant, and oversized material crushed in the tertiary crushers, it is also beneficiated through jigging in either the Lumpy or Fines Jig Plants, in order to remove any contaminants.
The final product is then stockpiled on the Lumpy, Fines or DR Lump product stockpiles, ahead of a rapid load-out station, to periodically load 342 x 100-tonne wagons, which are then railed for exporting purposes via the 861 kilometre Sishen-Saldanha railway line to the Port of Saldanha Bay on South Africa's West Coast, in the Western Cape Province.
On 12 August 2010, on the same day it confirmed that Khumani had been commissioned on time and on budget, the company’s directors approved additional capital expenditure of R5.5 billion for the completion of the Khumani Expansion Project, to increase the mine’s capacity to 16 million tonnes per annum.
The extension will see second primary and secondary crushers, screening systems and stockpile locations brought online at Assmang’s King property. In many respects, the new plant will simply mirror the existing one. To cope with the expansion, Transnet, which operates the dedicated rail line, has agreed to raise Assmang’s allocation from ten million to 14 million tonnes a year.
Every day of the year, a 342-wagon train leaves for Saldanha, with each wagon carrying 100 tonnes of ore. When the line was built back in 1976, it had an annual capacity of 18 million tonnes. Today, it can carry 60 million tonnes a year. Meanwhile, the port facilities at Saldanha are being similarly prepared, so by the time the downturn is over and the world’s steelmakers again struggle to meet demand, Assmang will be there to supply them with a better quality of ore than they can find anywhere in the world.
Written by Will Daynes, research by Richard Halfhide